Address
No. 3F07, Tao Cube, No.68, CCIH, Jihua West Road,Chancheng District, Foshan City, Guangdong, China.
Production Process Of Large Slab
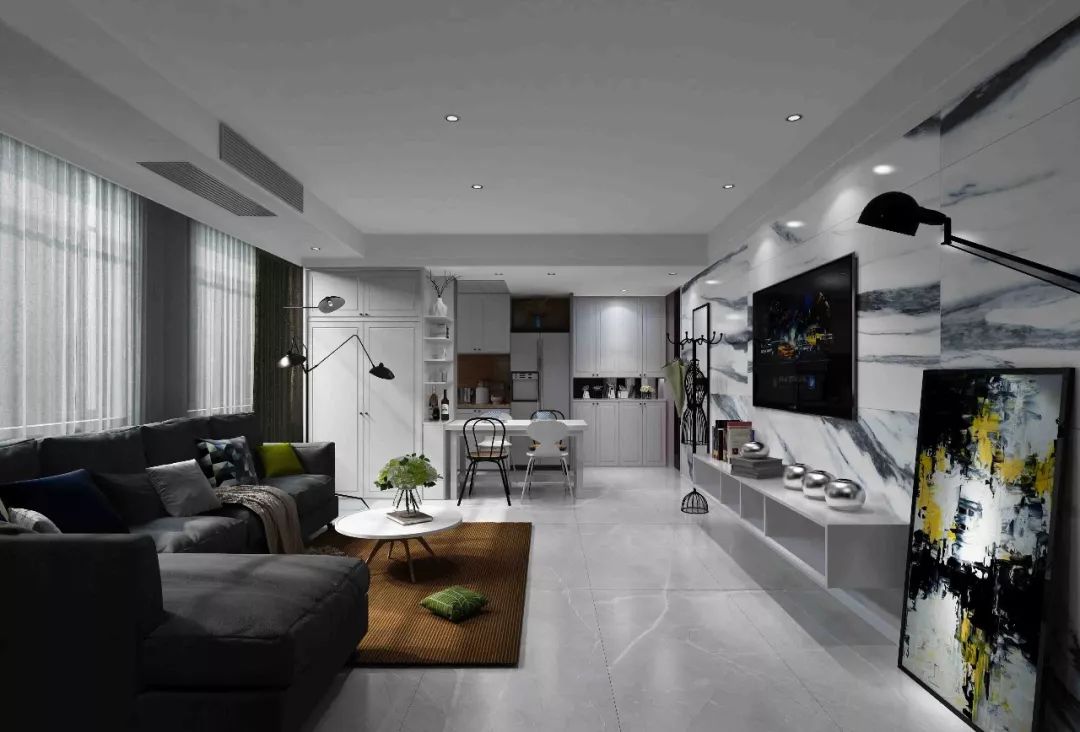
Raw Material Preparation
1.Whether it is warm sand, kaolin, black talc, cooked coke, low-temperature white sand, high-strength soil, etc., this is the first stop for them to transform into materials.
2. Carry out strict quality control on the raw and auxiliary materials of ceramic tiles. Only raw materials that pass standard testing can enter the batching process.
3. The raw materials that pass the test will be batched by the batcher according to the proportion and sent to the ball mill through the conveyor belt.
Biscuit Forming
Ball mill is the core link of raw material processing. The particles produced by ball milling determine the shape of the bricks, and the fineness of the particles and the averageness of the particles determine the quality of the ceramic tiles.
4. Ball milling
After 13-15 hours of ball milling, the mud has a fineness of 0.7-0.9. The ball-milled ingredients are added with water and then flowed out of the ball mill for iron removal and screening. The coarse particles that do not meet the requirements are separated and returned to the ball for re-ball milling.
5. Slurry storage
After the iron is removed and screened, it enters the slurry tank and is aged for later use.
6. Spray tower powder making
The evenly mixed slurry enters the spray drying tower through the automatic slurry conveying system. After hot air exchange, the dried and dehydrated particles have a diameter of 0.5-2 mm and contain 7% moisture. The spray-dried powder is sent to powder storage.
7. Press Forming
The powder is transported by the conveyor belt into the press and pressed into shape. Large-tonnage press Henlitai 16800-ton press can press large porcelain plates of various sizes from 900X900mm to 1200X2400mm.
8. Biscuit Drying
The pressed green body needs to be dried again in a drying kiln to reduce the moisture content to less than 0.5% before entering the next step.
9. Glaze
When the moisture content of the bricks drops below 0.5%, the “glaze pouring” step can be entered. Pour the glaze slurry into the high-level tank, and through the buffering effect of the glaze tank and the screen mesh, the glaze slurry passes through the smooth bell jar and evenly covers the surface of the body.
10. 3D inkjet printing
The glaze biscuit is sent to the inkjet printing machine through a conveyor belt, and the computer-preset pattern is directly printed on the surface of the glaze blank. An 8-channel inkjet machine creates realistic effects, and 3.6 million pixels truly restore the texture of natural marble. 360° color embryo full-body fabric technology makes the color texture of the surface and processing surface consistent, achieving large-area, high-fidelity, and seamless vision.
11. Kiln Firing
The roller kiln is 350 meters long and the firing temperature reaches 1200°C. According to the change of the kiln temperature, it is divided into preheating zone, firing zone and cooling zone. The firing time and temperature of each stage are strictly controlled by computer program. The glazed bricks are sent to the roller kiln by a conveyor belt and can be fired in just 70 minutes.
12. Cool down
At this time, the temperature of the bricks is very high and needs to be cooled. The cooled porcelain slabs are transported to the polishing workshop by the ceramic tile intelligent conveyor line.
The conveyor line consists of an upper and lower brick machine, an intelligent ferry transportation system and an orbital brick storage system, which realizes unmanned automatic transportation and storage, reduces costs and ensures stable operation.
13. Polish
After the ceramic tiles are fired and cooled, they enter the edge grinding process. After completing the edge grinding and sizing, the tiles enter the rough polishing machine and the medium polishing machine on the conveyor belt for polishing.
In order to improve the anti-fouling ability, a layer of nano-anti-fouling agent should be evenly coated on the surface of the ceramic tile. This forms a protective layer on the brick body with particles as small as nanometers. Porcelain slabs have unparalleled top-level anti-fouling properties. properties, abrasion resistance and high gloss.
14. Inspection and grading
Porcelain slabs will undergo both machine inspection and manual inspection. Employees on the assembly line carefully and carefully detect quality indicators such as color difference, flatness, and geometric dimensions, and then inspect and grade the products.
15. Packing
After inspection, the products enter the automatic packaging process: automatic film loading, automatic carton placement, automatic folding, automatic strapping, automatic palletizing, and a series of fully automatic processes. The large ceramic plates are perfectly packaged and transported to the warehouse.